Case Study: In Search of Flawless Execution – RT Moore’s Machine Vision Journey
Introduction
The Indiana AI Innovation Network connects leaders across industries to foster innovation and collaboration around artificial intelligence (AI.) With over 150 members statewide, the network convenes monthly, offering opportunities to share breakthroughs, explore case studies, and advance Indiana’s leadership in the AI space.
In Q2 2025, RT Moore, a long-standing innovator in mechanical contracting, partnered with AI consultancy Stellar to address one of construction’s most persistent and costly challenges: detecting quality issues before they result in expensive rework. With advances in AI becoming more accessible, RT Moore’s CIO, Josh Adams, asked a critical question: “Could artificial intelligence help catch these issues earlier; ideally, during rough-in construction, before they became expensive problems? And if so, where should RT Moore begin?”
This case study explores how RT Moore used AI-driven machine vision to transform its approach to quality control, increase operational efficiency, and lay the foundation for broader AI adoption.
Part 1: Industry Context & Business Challenge
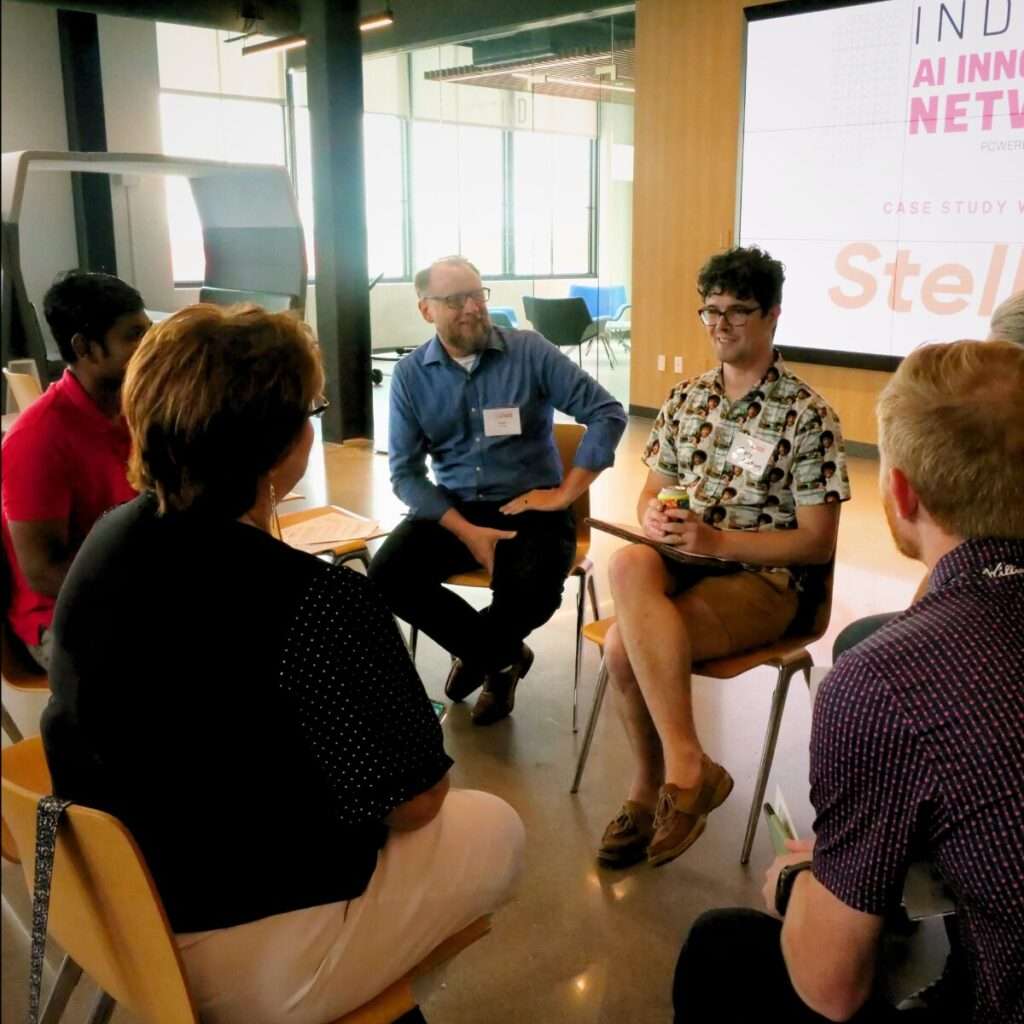
RT Moore, a $300 million mechanical contractor headquartered in Indianapolis, provides HVAC and plumbing solutions for single- and multi-family residential construction across Indiana, Ohio, Florida, and North Carolina. With a workforce of over 800 employees and a reputation for embracing technology, RT Moore continually seeks to improve project quality, reduce rework, and deliver on time and on budget.
Despite technological investments such as GPS tracking and project management systems, a recurring challenge remained: quality issues; often discovered late in the construction cycle that led to costly delays, rework, and reputational risk. These issues were especially prevalent in the “above ground rough-in” phase, where HVAC and plumbing systems are installed just prior to drywall. If quality issues are missed in the above-ground rough-in phase, the cost of remediation escalates quickly. By the time walls are closed, addressing a misplaced pipe or missing stud guard could involve days of work across multiple trades and cause substantial delays.
The question: Could AI-driven tools help RT Moore detect defects earlier while still in rough-in and prevent problems before they became liabilities?
Part 2: AI Implementation Strategy
RT Moore and Stellar set out to explore machine vision as a solution to detect construction errors automatically from field photos, thereby preventing costly rework and improving inspection workflows.
Approaches Considered:
- Manual Quality Control Enhancements: Increasing reliance on human-led photo review or on-site inspections.
- General Computer Vision Models: Using out-of-the-box AI models trained on generic construction imagery.
- Constrained Machine Vision System: Developing a tailored AI model using RT Moore’s own photo documentation to recognize specific quality markers within the rough-in phase.
The selected strategy focused on a constrained machine vision model, trained on labeled internal image data and integrated into RT Moore’s existing project management systems.
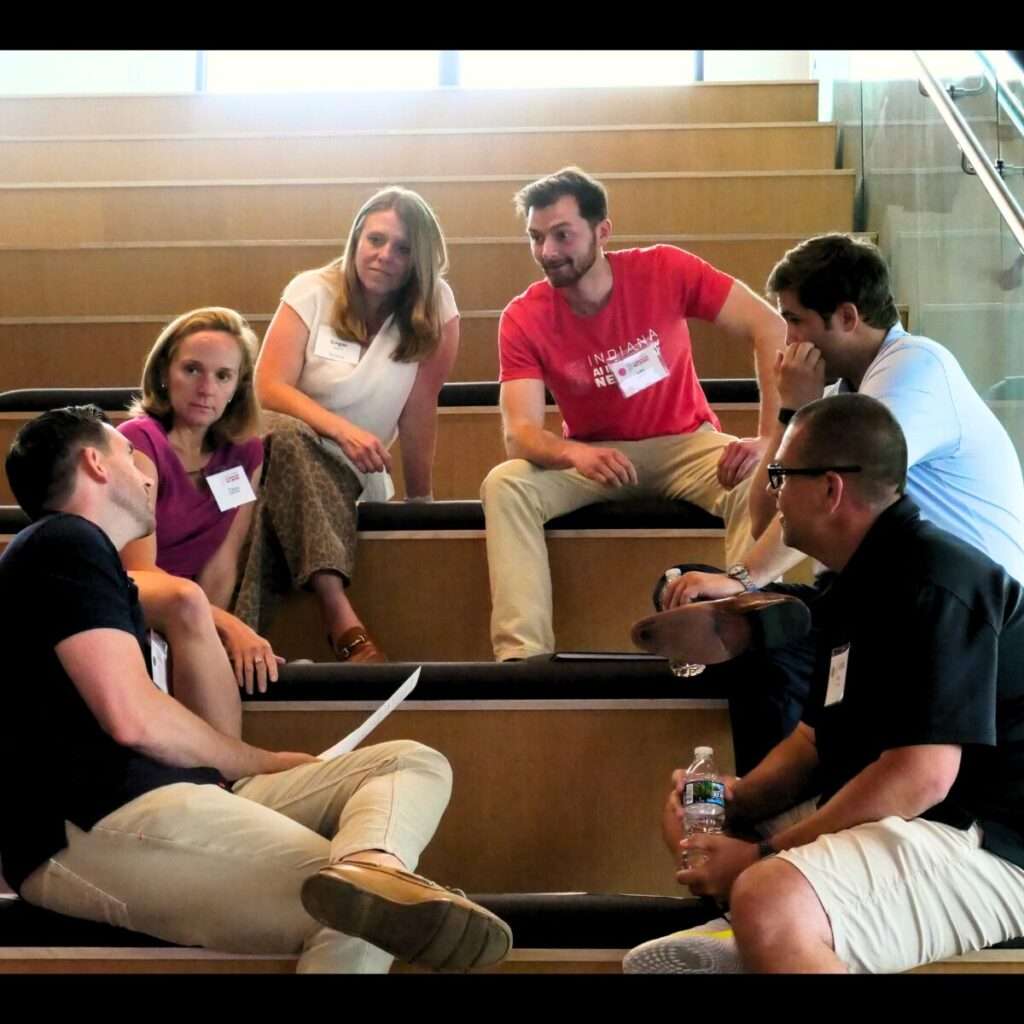
Part 3: Solution and Implementation
The project began with a proof-of-concept (POC) focused specifically on the high-impact “above ground rough-in” stage. The implementation emphasized constrained, domain-specific AI training to ensure relevance and accuracy.
Key Components:
- Defined Quality Standards: Engineers and project managers outlined key inspection criteria, such as pipe alignment, fixture leveling, presence of stud guards, and angles of pipe bends.
- Custom Image Dataset: Thousands of jobsite images, already being collected via body cameras and mobile uploads, were labeled as examples of “pass” and “fail” conditions.
- Model Development: A machine vision model leveraging large language models (LLMs) integrated with Azure OpenAI was trained to detect and classify quality issues.
- Workflow Integration: An Azure Function App was built to ingest new images automatically, analyze them, and populate results into RT Moore’s existing Azure SQL and Power BI environments.
Project managers now received proactive alerts when an image failed the AI quality check, allowing for timely reviews before drywall was installed. While the system still returned occasional false positives, the ease of validation (just reviewing the flagged image) made it a net productivity gain.
Part 4: Outcomes
Improved Defect Detection: The AI model successfully identified high-risk construction errors during rough-in, often before they were visible to the human eye.
Operational Efficiency: The system enabled proactive issue resolution and reduced the reliance on manual inspections improving team productivity without disrupting workflows.
Scalable Infrastructure: By building the model within their existing Azure ecosystem, RT Moore created a foundation for future AI applications across job phases and business functions.
Cost Avoidance: Early detection of quality issues helped avoid significant rework costs each prevented error potentially saving thousands of dollars and avoiding project delays.
Conclusion
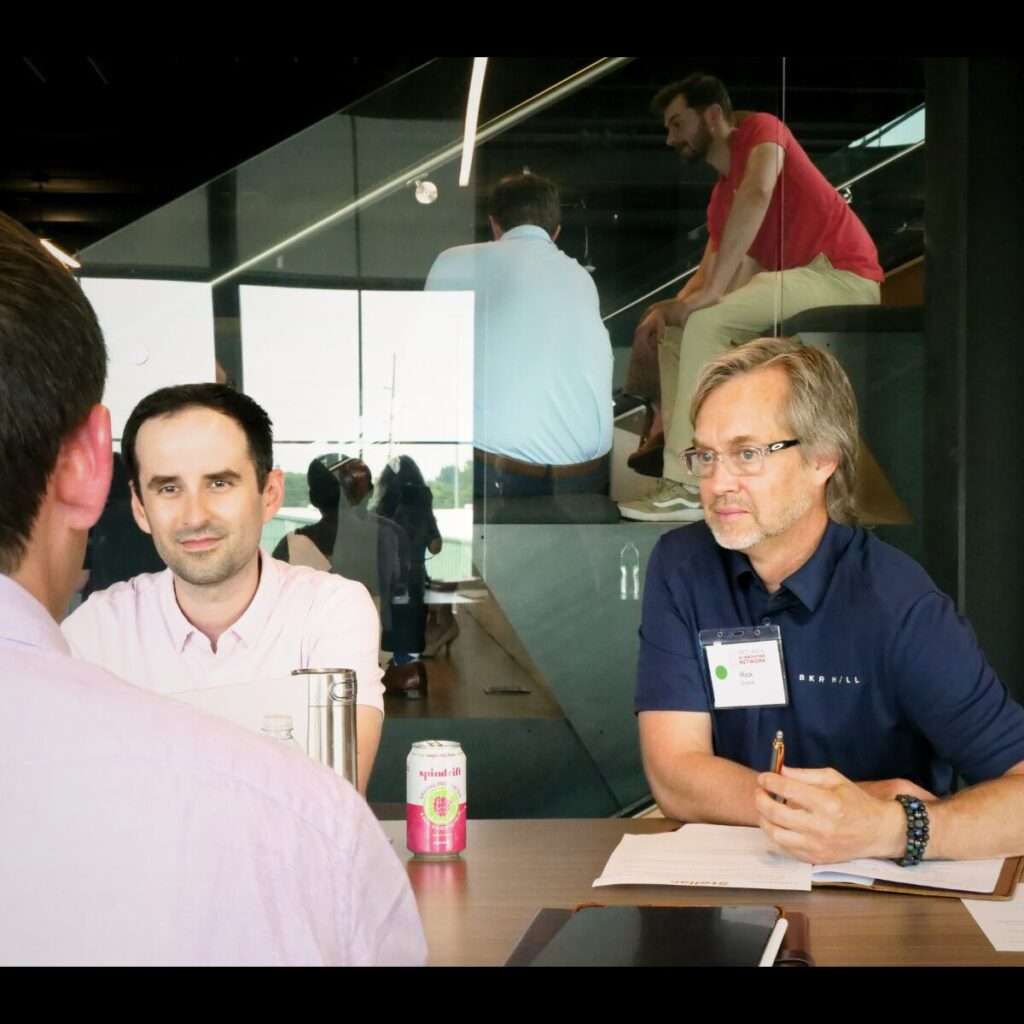
The constrained, domain-specific approach taken in this pilot has become a model for future deployments. Beyond operational improvement, the machine vision project signaled a broader shift in RT Moore’s strategy. With this success under their belt, the team began exploring additional use cases for AI; such as identifying improperly secured pipes during pea-fill or classifying images by job phase automatically.
As Josh Adams, CIO of RT Moore, reflected, “This was our first AI win. It won’t be the last.”
Through disciplined constraint, targeted implementation, and integration with existing workflows, RT Moore’s journey illustrates how AI can solve entrenched problems without overcomplicating solutions. Their experience highlights the power of applying AI in focused, strategic ways that align with real business needs.
Written by: Zach Linder (Stellar) and Mary Dougherty (TechPoint)